oee的计算实例,设备效率计算公式和规格要求一致嘛
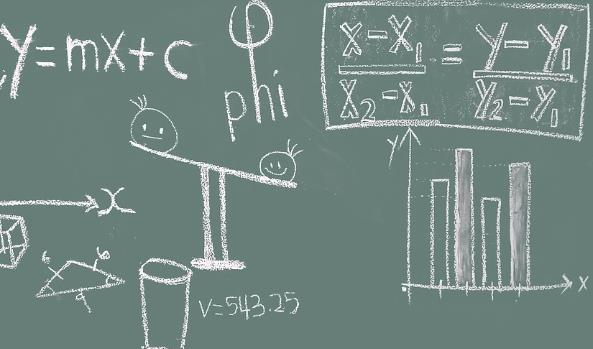
oee的计算实例?
注:标准节拍时间为3min计算:停机时间 = 115+12 = 127 min计划开动时间 = 910 □ 127 = 783 min时间开动率 = 783/910 = 86%计划节拍数 = 开动时间/标准节拍时间 = 783/3 = 261性能开动率 = 203/261 = 77.7%合格品率 = 一次合格品数/完成产品数 = 152/203 = 74.9%于是得到OEE = 86% ×77.7%×74.9% = 百分之50OEE的表达和计算公式:
我们举一个例子来说明OEE的计算方式:设某设备某天工作时间为8h, 班前计划停机15min, 故障停机30min,设备调整25min, 产品的理论加工周期为0.6 min/件, 一天共加工产品450件, 有20件废品, 求这台设备的OEE。按照上面就可以清楚的知道:计划运行时间=8x60-15=465 (min)实质上运行时间=465-30-25=410 (min)有效率=410/465=0.881(88.1%)生产总量=450(件)理想速度x实质上运行时间=1/0.6 x 410=683表现性=450/683=0.658(65.8%)(另外解法:表现性=理想加工周期*生产数量/实质上运行时间=0.6*450/410=0.658(65.8%))质量指数=(450—20)/450=0.955(95.5%)OEE=有效率x表现性x质量指数=55.4%另一种OEE算法:OEE=满足质量要求的产品/大理论产量此例中大理论产量=(8*60-15)/0.6件=775件满足质量要求产品=450-20=430件OEE=430/775*百分之100=55.4%OEE的作用实践证明OEE是一个极好的基准工具,通过OEE模型的各子项分析,它准确了解地告诉你设备效率如何,在生产的哪个环节有多少损失,还有你可以进行那些改善工作。达到提升生产效率的目标,同时使公司不要没有必要要的耗费。
设备效率计算公式?
生产效率=(生产数量÷生产实质上人员数量)÷(标准小时产能×生产时长÷标准人员数量)
实质上产量:生产部、财务计算生产效率/生产力时以实质上入库量计算。
挡产工时:因外部门或受客观条件影响导致停线或返工工时。
加班工时:为增多产量而延长的工作时间。
扩展资料
1、提升工作效率可以增多二者利益。即促进单位的劳动生产率和经济效益的提升,增多活力;促进工作人员个人达到多劳多得,增多收入。
2、提升工作效率以后,就有可能缩短工作时间,以此有更多时间让员工自行支配,去从事学习、娱乐、旅游、社交和休息。
3、提升工作效率以后,可以克服机构臃肿,人浮于事,浪费时间的情况。
4、提升工作效率后面,在优化劳动组合中,具有更大的竞争优势。
OEE名词定义还有计算方式
OEE=可用率(B/A)×表现指数(C/B)×质量指数(E/D)
日历工作时间
计划中断
A 负荷工作时间 设备 保养 计划停工待料 计划 停产 休息就餐
停机
B 实质上运行时间 品质 确认 设备 调整 产品 换型 交接班 设备 故障 停工 待料 其他 损失
速度损失
C 正常(无损失)运行时间 设备 空转 减速 损失 暂停 损失
D 生产数量
浪费
E 合格品数 开始过程次品损失 生产过程次品损失
OEE
定义:Overall Equipment Effectiveness(全局设备效率)的缩写,它由可用率,表现指数还有质量指数三个重要要素
组成。
计算方式
OEE=可用率X 表现指数 X质量指数
可用率=实质上运行时间 / 负荷工作时间
可用率:它是用来考虑停工所带来的损失,涵盖导致计划生产出现停工的任何事件,比如设备故障,原料短缺还有生产
方式的改变等。
表现指数=(净CT时间*生产数量)/实质上运行时间
表现指数: 表现性考虑生产速度上的损失。涵盖任何致使生产不可以以大速度运行的原因,比如设备的磨损,材料的不
合格还有操作人员的失误等。
质量指数=合格品数/生产数量
质量指数: 质量指数考虑质量的损失,它用来反映没有满足质量要求的产品(涵盖返工的产品)。
负荷工作时间:除去设备休止以外班别正常工作时间(出勤时间)
实质上运行时间:除去停机损失之外的计划生产时间
产线与PMC
1 理想节拍时间=净Cycle time时间
定义:生产线正常运转(无停机和速度损失)状态下,单个工位完成一次都作业内容所需时间(实质上测算CYCLE
TIME=生产线无法提升的尴尬境地工位完成一次都作业内容所需时间)
SMT是机器正常生产(前后也都没有供应不上和堵塞的情况)情况下从一片板夹住启动贴装到第二片板夹住启动贴装
为一个周期时间。
MIMA、FA、FG是正常情况单个工位完成一次都作业内容所需时间。
2 Standard time(标准节拍时间) - 设定线速使用
定义:普通熟练的作业员在正常情况下,以合理的劳动强度和速度,合理的操作方式,完成满足质量要求的产品所需时间
计算方式:
标准节拍时间(ST)=净CT时间*(1+T.A.F)=净CT时间*(1+生理宽放+疲劳宽放+管理宽放)
3 设备有效运转率
计算方式:
设备有效运转率(%)= 正常(无损失)运行
设备利用率=每班次(天)实质上开机时数/ 每班次(天)应开机时数*百分之100
oee理论加工周期怎么算?
因为单件加工时间比较长,故此,不计算每天或每班的OEE,直接计算阅读OEE。
假设:每月上班26天,每天三班,每班8小时,理论单件CT时间8小时。
既然如此那,
每月计划开机时间=26*3*8=624小时(不考虑中间休息时间,当然实质上有,可以计算在内)
每月计划生产量=624/8=78件
例如1月份生产了75件产品,这当中1件不合格品,1月份停机3小时(维修或处理质量问题)。
既然如此那,
一次通过率(FTT)=(75-1)/75×百分之100=98.6%(乘百分之100是将得数转化为百分比的意思)
利用率=(634-3)/624×百分之100=99.5%
性能效率=(理论CT时间×生产数量)/实质上开机时间=8×75/(624-3)×百分之100=96.6%
注:性能效率的意思是:生产固定数量产品,理论时间和实质上时间的比率。
综合效率OEE=一次通过率×利用率×性能效率=98.6%×99.5%×96.6%=94.77%
大多数情况下OEE高于85%已经属于全球级别的制造工厂了,上面举例的OEE达到94.77%是假设30天以来实质上开机率很高,而且,合格率也很高的情况才出现,你可按你们公司实质上的开机时间和合格率来计算。
设备性能开动率公式?
设备综合效率OEE计算公式和方式实例 影响设备综合效率的重要因素是停机损失、速度损失和废品损失。
它们分别由时间开动率、性开动率和合格品率反映出来,故得到下面设备综合效率公式: 设备综合效率=时间开动率×性能开动率×合格品率 这里,负荷时间为规定的作业时间除去每天的停机时间,即 负荷时间=总工作时间-计划停机时间 工作时间则是负荷时间除去那些非计划停
OEE在工厂里代表什么意思?
(OEE) 什么是OEE 认识OEE的三个构成原因:可用水平,运行水平,质量水平 OEE...有效地挖掘潜藏在工厂内部的“黄金”,是每一个工厂管理人员需要承担的永恒的...生产企业基本状况分析(左面为反映的代表情况,右面为课程提供的基本处理思路) 思想...
大多数情况下,每一个生产设备都拥有自己的大理论产能,要达到这一产能一定要保证没有任何干扰和质量损耗。 实质上生产中是不可能达到这一要求,因为许不少多的原因,车间设备存在着非常多的失效: 比如,除去设备的故障、调整,还有设备的完全更改替换之外,当设备的表现很低时,可能会影响生产率,出现次品,返工等。
我们举一个例子来说明OEE的计算方式: 设某设备某天工作时间为8h, 班前计划停机15min, 故障停机30min,设备调整25min, 产品的理论加工周期为0.6 min/件, 一天共加工产品450件, 有20件废品, 求这台设备的OEE。 按照上面就可以清楚的知道: 计划运行时间=8x60-15=465 (min) 实质上运行时间=465-30-25=410 (min) 有效率=410/465=0.881(88.1%) 生产总量=450(件) 理想速度x实质上运行时间=1/0.6 x 410=683 表现性=450/683=0.658(65.8%) (另外解法:表现性=理想加工周期*生产数量/实质上运行时间=0.6*450/410=0.658(65.8%)) 质量指数=(450—20)/450=0.955(95.5%) OEE=有效率x表现性x质量指数=55.4%
机器设备使用效率的指标?
企业里,用于度量设备管理好坏的指标不少。比如设备的完好率,设备的可用率,设备综合效率,设备完全有效生产率,设备故障率,平均故障间隔期,平均修理时间,设备备件库存周转率,备件资金率,维修费用率,检修质量一次合格率,返修率等等。不一样的指标用于度量不一样的管理方向。
设备管理的指标评价:
1. 设备的完好率
在这些指标里用得多,但其对管理的促进作用有限。
这里说的的完好率是在检查这个时间段,完好设备与设备总台数的比例(设备完好率=完好设备数/设备总数)不少工厂的指标可以达到95%都。理由很简单,在检查的那一刻,假设设备是运转的,没出故障,就算是完好的,于是这个指标就很好看。很好看就算是没有多少可提高的空间了,就算是没啥可改善的了,那就说明超级难进步了。
针对这个问题,很多企业提出对这一指标的定义进行改造,比如提出每月8日,18日,28日检查三次,取其完好率的平均值作为本月的完好率。这当然比检查一次要好,但也还是是点状反映出的完好率。后来有人提出以完好的台数数比上日历工作台时数,完好台时数等于日历工作台时减去故障及其修理的总台时数。
这个指标要真实多。当然又碰见统计的工作量增多和统计的真实性,碰见预防性维修台时是不是扣除的争论。完好率这一指标是不是有效反映设备管理状况,这要看如何应用,仁者见仁,智者见智。
2. 设备的故障率
这个指标容易混淆,存在两种定义:
假设是故障频率则是故障次数与设备实质上开动台时的比值(故障频率=故障停机次数/设备实质上开动台数);
假设是故障停机率,则是故障停机台时与设备实质上开动台时加上故障停机台时的比值(故障停机率=故障停机台时/(设备实质上开动台时+故障停机台时))
明显,故障停机率比较可以真实的反映设备状态。
3. 设备的可用率
在西方国家采取有点多,而在我们国内有计划时间利用率(计划时间利用率=实质上工作时间/计划工作时间)和日历时间利用率(日历时间利用率=实质上工作时间/日历时间)两个不一样提法。
根据定义,西方定义的可用率其实是日历时间利用率。日历时间利用率反映了设备的完全利用状况,其实就是常说的说就算是单班运行的设备,我们也根据24小时计算日历时间。因为不管工厂是不是使用这台设备,都以折旧形式消耗着企业的资产。
计划时间利用率反映了设备的计划利用状况,假设是单班运行,其计划时间就是8小时。
4. 设备的平均故障间隔期
MTBF的另外一个提法叫做平均无故障工作时间(设备平均故障间隔期=统计基期无故障运行总时间/故障次数)。它与故障停机率互补的反映了故障频次,其实就是常说的设备的健康状况。两个指标取一个完全就能够了,没有必要利用有关指标度量一个内容。
另外一个反映维修效率的指标是平均修理时间MTTR(平均修理时间=统计基期维修消耗的总时间/维修次数),它度量的是维修工作效率的改善状况。
随着设备技术进步,其复杂程度、维修难度、故障部位、维修技师的平均技术素质还有设备工龄的不一样,维修时间超级难有确定的数值,但我们可以据此度量其平均状况和进步状况。
5. 设备综合效率
OEE是比较全面反映设备效率的一个指标,OEE是时间开动率、性能开动率与合格频率的乘积。就像一个人,时间开动率代表出勤率,性能开动率代表上班后是不是努力工作,发挥出应有的效率,合格品率代表工作的有效性是否常常出差错是否可以保质保量完成任务。
简单的OEE公式就是:设备综合效率OEE=合格品产量/计划工作时间的理论产量
6. 完全有效生产率
TEEP是可以彻底反映设备效率的公式而不是OEE。完全有效生产率TEEP=合格品产量/日历时间的理论产量,这一指标将设备的系统管理缺陷,涵盖上下游影响、市场和订单影响、设备产能不平衡、计划具体安排调度的不合理等不够都反映出来。这个指标大多数情况下都很低,不好看,但十分真实。
维修及其管理方面:
7. 检修质量一次合格率
是用检修后的设备试运行一次达到产品合格标准次数比上检修次数来度量。工厂是不是采取这个指标作为维修团队Team的绩效指标,可以研究推敲。
8. 返修率
是设备检修后返修总次数比上检修总次数。这比较真实反映检修质量。
9. 维修费用率
它的定义和算法不少,一种是年维修费与年总产值比,另外一种是年维修费与当年资产总原值比,还有一种是年维修费与当年资产总重置费比,再有一种是年维修费与当年资产总净值比,后一种是年维修费与当年生产总费用比。
就算如此,这个维修费用率数值的大小又不可以够说明问题。因为,设备维修是一种投入,投入是创造价值和产出的。投入不够,生产损失突出,则影响产出; 投入太大也不太好,称为维修过剩是一种浪费。合适的投入理想。
故此工厂应该摸索和研究好的投入比例,生产费用高算是订单多,任务量大,而且,设备的负荷加大,对维护保养的需求也随之上升。在合适的比例上投入是应该工厂努力追求的目标。假设有了这个基准,偏离这个指标越远就越不太好。
备件管理指标:
10. 备件库存周转率
(备件库存周转率=月消耗备件费用/月平均备件库存资金)是较代表性的指标。它反映了备件的流动性。
假设非常多库存资金积压,则会在周转率上反映出来。反映备件管理的还有备件资金率,即都备件资金与企业设备总原值之比。这个数值的高低随着工厂是不是在中心城市、设备是不是进口,设备停机损失影响大小而不一样。
假设设备一天的停机损失高达几千万元,或者故障对环境污染危害严重,对人身安全危害突出,而备件供货周期较长则备件库存量就要高些,反之这个备件资金率就尽量降低
11. 维修培训时间强度
(维修培训时间强度=维修培训小时/维修工时)培训涵盖设备结构专业知识、维修技术、职业素养和维修管理等内容。这一指标反映了企业对维修人员素养提高的重视程度、投入强度,也间接反映了维修技术能力水平。

>>二级建造师培训班视频课程,听名师讲解<<
相关推荐: