加工中心主轴转速的计算方法,螺纹加工转速计算公式
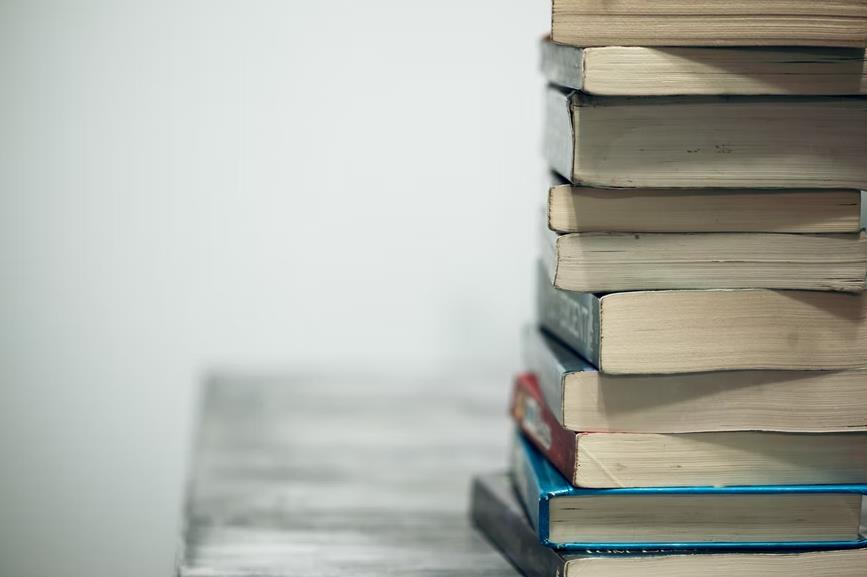
加工中心主轴转速的计算方式?
主轴转速有两种计算方式,下面举例说明:(1)主轴转速:一种是G97 S1000表示一分钟主轴旋转1000圈,其实就是常说的一般所说的恒转速。
另一种是G96 S80是恒线速是由工件表面确定的主轴转速。进给速度也有两种G94 F100表示一分钟走刀距离为100毫米。另一种是G95 F0.1表示主轴每转一圈,刀具进给尺寸为0.1毫米。
数控加工中心的切削转速和进给速度:
1、主轴转速=1000Vc/πD
2、大多数情况下刀具的高切削速度(Vc):高速钢50 m/min;超硬工具150 m/min;涂镀刀具250 m/min;陶瓷·钻石刀具1000 m/min 3加工合金钢布氏硬度=275-325时高速钢刀具Vc=18m/min;硬质合金刀
加工转速计算公式?
1.第一你要记住这个公式:切削速度=(加工直径*3.14*转速)/1000
2.主轴的转速,进给量,和切削量主要还是由刀具决定,加工同样的材料性能不一样的刀具,他的参数也明显不同,不清楚你是用什么牌子的刀具。我们用三特维克的刀具,他的刀片都会提供加工不一样材料的参数,例如大进给量,切削量和切削速度。
3.例如你加工直径40的孔,刀具的大切削速度是150米/分。
计算主轴转速:S=(150/3.14/40)*1000=1194转
转速进给计算公式?
主轴转速n=Vc*1000/(π*Dc)例子:已知一百主轴转速度为1350rev/min,钻头直径为φ12mm,则切削线速度Vc=n*π*Dc/1000=1350*3.15*12/1000
=50.9mm/min。
主轴进给速度vf=n*f例子:专每转进属给为0.2mm/rev,主轴转速为1350rev/min,则vf=n*f=1350*0.2=270mm/min
主轴转速怎么表示?
1、用于主轴旋转速度控制的代码是S。
2、主轴转速为机械类产品主轴的转速。譬如硬盘,非常高的转速可缩短硬盘的平均寻道时间和实质上读写时间,以此提升硬盘的数据传输速度。主轴转速应按照允许的切削速度和工件(或刀具)直径来选择。在加工时确定主轴转速是很重要的一个环节,它直接关系到刀具寿命,工件加工效果等
r/min表示每分钟多少转。r/s表示每秒钟转多少转 另外min是minute的缩写,s是second的缩写,h是hour的缩写。分别表示分钟 秒 小时
每分钟进给量的计算公式?
G99每转进给单位是mm/转,G98每分进给mm/分钟,G98模式下每分钟的进给量除以转速等于G99的每转进给。普车的是每转的进给量。 F=转速*走刀量*一分钟(普车),数控铣床两种都可以,看你用那个g代码。
车床 线速度=3.14*工件直径*转速(s) 每分进给速度f=每转进给速度*转速s。
铣床 刀片线速度=3.14*刀具标称直径*主轴转速s 每分进给速度F=每齿进给量*齿数*主轴转速(n) 单位米和毫米要弄准
切削速度=(3.14*工件待加工面直径(毫米)*工件每分钟转数)/1000进给量:是指工件每转一转,刀具沿进给方向移动的距离(也称走刀量),单位是(毫米/转)。车床切削进给量是按照加工的外形尺寸和所加工的材料而定的,这个是要查手册的。
此外切削速度和进给量是和材料硬度、工件直径、切削系统刚性等原因相关的,且相互影响,不是简单靠公式来计算的,需实践经验的累积。 期望对你有很大帮助。
分钟进给量=每转进给量×主轴每分钟转数。进给量与工件变形区中的变形量直接相关。当进给量较小时,变形量也较小,变形渗透不到工件内部,加剧金属变形的不均匀性,影响锻件质量。
对圆柱件摆碾时,进给量太小时会出现“蘑菇效应”。
为保证锻件质量,要有足够的进给量,以使变形能渗透到整个锻件高度。
精车时,加工精度和表面粗糙度要求非常高,加工余量不大且较均匀,因为这个原因选择精车的切削用量时,应着重新再来考虑如何保证加工质量,并在这里基础上尽可能提升生产率。扩展资料:
4、刀具空行程时,非常是远距离“回零”时,可以选择该机床数控系统设定的高进给速度。
额定转速计算公式?
1. 额定转速 = 60*50/2 就是60乘以工频 50赫兹 除以磁极对数 其实就是常说的说你的电机是四级的 两对磁极。
2. 同上 其实就是常说的 10对磁极 60*50/10=30 转/每分钟
3.估计是钉子通电以后 转自会转 转的途中的这个磁场 也可觉得是旋转磁场,这个磁场对定子的作用 假象的觉得定子也可转 但是,其实是不转的, 应该有正负 可以抵消掉 和转差率差很少
4.这个没办法解释 除非定子旋转 转子不转 这样的结构唯有大型发电机是这样的结构
5.那就是说转子不转了
计算公式为转速n=60f/p,n表示转速,f表示频率,p表示电机的极对数。
发电机转速是发电机主轴的旋转速度,一分钟内所能完成的大转数。转速的快慢是标示发动机档次的重要参数之一,它是决定发动机内部传输率的重点原因之一。发电机的转速一般都以转/分来表示,符号记法r/min。
线速度和转速
线速度也有平均值和瞬时值之分。假设所取时间间隔很小很小,这样得到的就是瞬时线速度。
注意,当△t足够小时,圆弧AB基本上是直线,AB弧的长度与AB线段的长度基本上没有差别,这个时候,△l其实就是常说的物体由A到B的位移。因为这个原因,这里的v实际上就是直线运动中的瞬时速度,不过现目前用来描述圆周运动罢了。
线速度是矢量,有大小和方向,做圆周运动的物体,它的线速度方向时刻改变,并自始至终指向该点的切线方向。
转差率=(同步转速-异步转速)/同步转速 同步转速=60*电源频率/极对数 大转矩、额定转矩=额定功率/额定转速/9550 任意转速下的转矩=2*大转矩/(转差率/大转矩时的转差率+大转矩时的转差率/转差率) 当转差率小于额定功率时的转差率时 任意转速下的转矩=2*大转矩*转差率/大功率转矩时的转差率 额定电功率=额定电压*额定电流
cnc线速度的计算方式?
这里说的线速度就是刀片和工件接触位置的相对速度。
针对车床来说是刀具不动(进给速度在这里可以忽视不计)工件旋转,故此,工件和刀具的接触位置的速度就是切削线速度,即:
V=Pi*D*n/1000,这当中Pi是圆周率,D是刀具和工件接触点的旋转直径,n是主轴转速。n的单位是 转/分,D的单位是毫米,后结果V的单位是米/分。
针对加工中心来说是工件不动(进给速度在这里同样可以忽视不计),刀具旋转,故此,刀尖的速度就是线速度,计算公式也是:
V=Pi*D*n/1000,这当中Pi是圆周率,D是刀尖位置的实质上旋转直径,n是主轴转速。
从这两个计算公式可以看得出来线速度和进给F还有切深是无关的。
因为作为刀片,切削的线速度是重要,要优先集中精力的参数之一,因为这个原因在刀具的说明书上,针对不一样的切削要求都会给出对应的切削线速度。在编程时,编程人员需按照切削的实质上情况再按照线速度计算出主轴的转速来编制程序。
在车床编程指令中,有恒线速切削指令,这个时候可以直接指定线速度,CNC会按照切削点直径的变化自动调整主轴转速。
数控车床车削螺纹转速公式?
主轴转速过高会·因系统响应不上使螺纹乱牙。推荐主轴转速应满足下式: N*P3000这当中N表示转速(单位:转/分)高转速小于2023P表示螺纹导程(单位mm)大多数情况下达不到这么高的速度,这和你的车床相关系。

相关推荐:
-
加工中心主轴转速的计算方法,螺纹加工转速计算公式
加工中心主轴转速的计算方式? 主轴转速有两种计算方式,下面举例说明:(1)主轴转速:一种是G97 S1000表示一分钟主轴旋转1000圈,其实就是常说的一般所说的恒转速。 另一种是G96 S80是恒线速是由工件表面确定的主轴转速。进...
2022-11-06
-
后付年金终值怎么求,等额支付现值公式推导
后付年金终值怎么求? 后付年金终值就是普通年金终值 =A(F/A,i,n) A为每一年支付的钱 i为折现率 n为期限。 后付年金终值:指一定时期内,每期期末等额收入或支出的本利和,其实就是常说的将每一期的金额,按复利换算到后一...
2022-11-06
-
excel表格怎么往下拉公式不变,公式不能下拉复制
excel表格怎么往下拉公式不变? 1、使用的绝对引用。$符号在行前面行不随公式的下拉而改变,假设在列前面,列不会变化在,行列前面,单元格不随公式而变化。 2、使用是手动计算功能。公式-计算-手动,大多数情况下默觉得自...
2022-11-05
-
P值怎么求,数学莱布尼茨公式是什么时候学的
P值怎么求? P值的计算公式是 P=2[1-Φ(z0)] 当被测假设H1为 p不等于p0时;P=1-Φ(z0) 当被测假设H1为 p大于p0时;P=Φ(z0) 当被测假设H1为 p小于p0时。总而言之,P值越小,表达结果越显著。 统计学中回归分析的主要内容为: 1、从一组数据...
2022-11-05
-
年份公式是什么,年份怎么算天数
年份公式是什么? 有关公元纪年的计算方式: 一、世纪 100年一个世纪,百位前面数值加1, 例子:1069年(王安石启动变法),10+1=11,故此公元11世纪; 例子:公元前221年(秦朝建立),2+1=3,故此公元前3世纪; 例子:公元前2...
2022-11-05